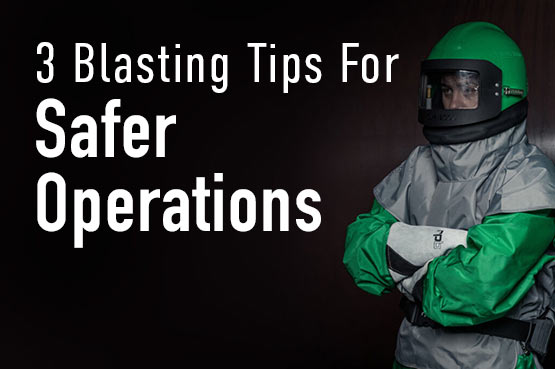
3 Tips to Keep Your Blast Operation Safe
In this blog, we’ll share three essential tips to help keep your blast operation safe, drawing from our experience supporting pros in the field. We’ll also highlight how our trusted lineup of RPB Safety gear, including the NOVA 3 respirator, Radex Airline Filter, GX4 CO/Gas Monitor, and proper breathing air hoses, can play a key role in maintaining a safe work environment.